Contact@1sourceADAS.com
Learn what to grab, and when to grab it!
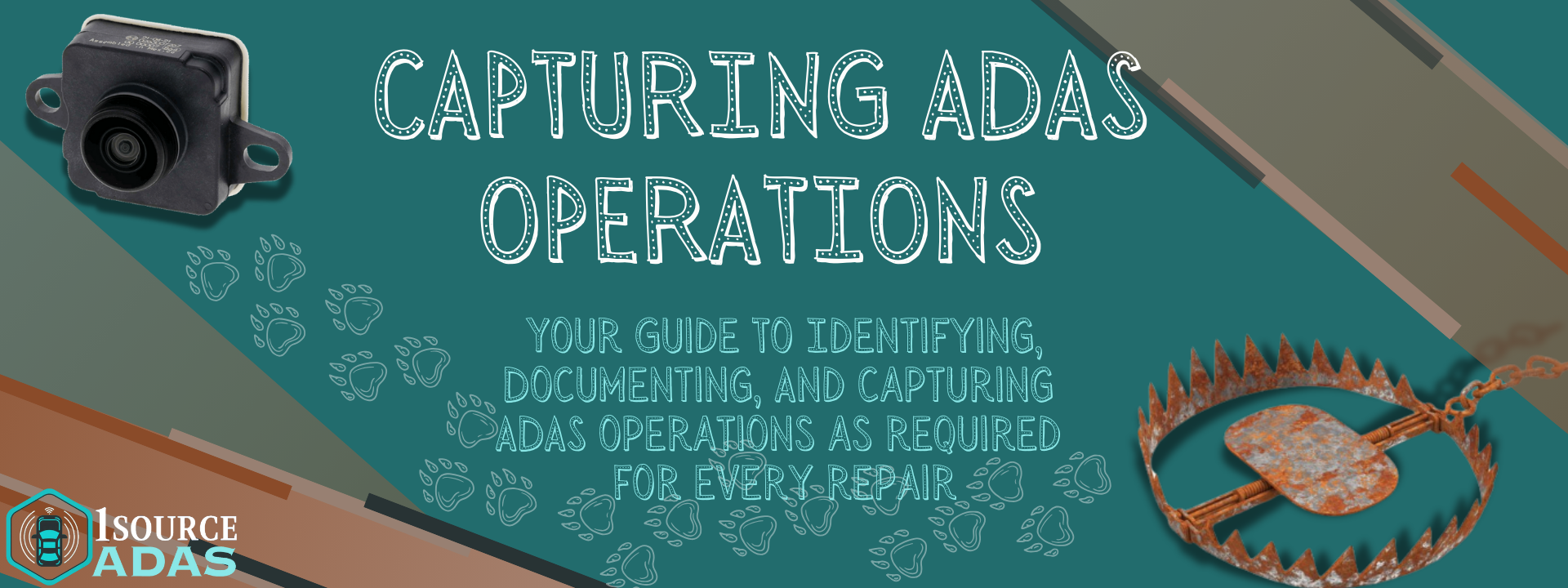
You’ve completed your estimate, run it through 1Source ADAS, and received the report. Now what?
If you’re like many shop owners, ensuring ADAS services are correctly completed for your customer can be challenging. ADAS service adds a unique stage to the repair process, demanding dedicated space, equipment, and special conditions. Honestly, sometimes, dealing with ADAS can be a pain point that’s difficult to manage. The good news is that it doesn’t have to be!
Let’s look at how you can remove the pain from the process and make it profitable while you’re at it.
Timing is Everything
There’s no better way to tempt fate than to call your ADAS service provider to do scans and calibrations when the vehicle is in the wash bay. Calibrations can fail for any number of reasons. A bad module, unseen damage, and incompatible aftermarket parts are just a few of the hazards that can come into play. Discovering these issues on the front end of the repair will prevent headaches later in the process. So, when should you be building your calibration plan?
- Proper ADAS capture should start with a pre-scan completed before disassembly. Disassembling the vehicle can create additional codes that can muddy the waters when determining the required operations.
- Unless you provide in-house ADAS service, having your ADAS service provider involved in the blueprint process can be invaluable. They don’t necessarily need to be onsite for it, but the blueprint is a good time to let them know what’s coming in the workflow.
- Once the vehicle is disassembled, start the blueprint process. This team effort between the estimator and technician is important and ensures that all the damage is captured. A complete estimate at this stage will allow you to determine the required ADAS operations and provide a launchpad for a smooth repair process.
- A critical step in the blueprint process is finding and reviewing all the procedures relevant to the repair. During the review, ensure you add the procedure operations to the estimate. Even if something is included, noting that you’re doing it helps document the process for anyone who sees your estimate.
Documentation is Also Everything
The estimate is complete once all the damage has been identified and added, procedures are reviewed, and required calibrations are identified. For a reviewer, the estimate is often like a table of contents. Each major operation should have supporting documentation, whether photos, an OEM procedure, or both. Copies of this documentation should accompany the estimate wherever it goes. This means having procedure PDFs in the estimating system and printed copies in the vehicle for the technician to reference.
It’s crucial to capture everything on the estimate and ensure every team member involved in the repair knows the requirements and completes their part. For a more in-depth look at repair documentation best practices, check out our documentation "If a Calibration Occurs Without Documentation, Did it Happen?".
Defending Your Documentation
Having documentation is not always enough. Before submitting an estimate for approval, ensure you’ve read and understand the procedures required for the repair. You’ll often be required to explain the documentation to a reviewer. While this may be as simple as saying, “because the manufacturer says so,” more detail is often required. Be prepared to explain how the involved systems work together, even if only at a basic level.
Remember, once the repair plan is complete, you must present it to the customer and insurer. The vehicle owner is the customer and absolutely must approve the repairs needed for their vehicle. Detailed documentation provides transparency to the customer, showing them exactly what was done to their vehicle and why it was necessary. This can build trust and enhance their overall satisfaction with your shop.
The insurer typically pays for the majority of the repair, so having them on board is also critical. Starting a repair is unwise until all parties agree to the repair plan. Unapproved repairs are the quickest path to unpaid work.
Planning Services
Once the repair plan is complete and approved, scheduling the segments of the repair process can begin. If you service ADAS in-house, this is likely a minor issue. If you utilize mobile or offsite calibration service providers, this is the time to engage them. One benefit of a complete blueprint is knowing when the repair will be complete. This information allows you to schedule ADAS services ahead of time, ensuring you can have the vehicle complete when promised. It also avoids the white knuckle scramble in the washbay when things go wrong.
Making ADAS Easy
For many shops, finding the required operations for the repair can be the most complex and time-consuming part of the process. This is where the 1Source ADAS platform simplifies the process. Our AI-powered system can read your estimate and utilize advanced algorithms to match your repairs with the OEM-required calibrations, pre-calibration requirements, and safety inspections. These are all provided to you in a single, easy-to-use report. Each report has direct links to the requirement data and the procedure, ensuring that your ADAS documentation is complete and that you always capture the necessary calibrations. Our intuitive interface makes it easy for anyone in your shop to use, regardless of their ADAS experience.
Getting started is easy. Simply click “Log In or Sign-Up” at the top of the page. Your first seven days are free; we only bill for the report. There are no contracts, no minimums, and we never dictate pricing or share your information. Start saving time and capturing profitable additional operations today with 1Source ADAS.