Contact@1sourceADAS.com
If It's Not In The File, It Didn't Happen.
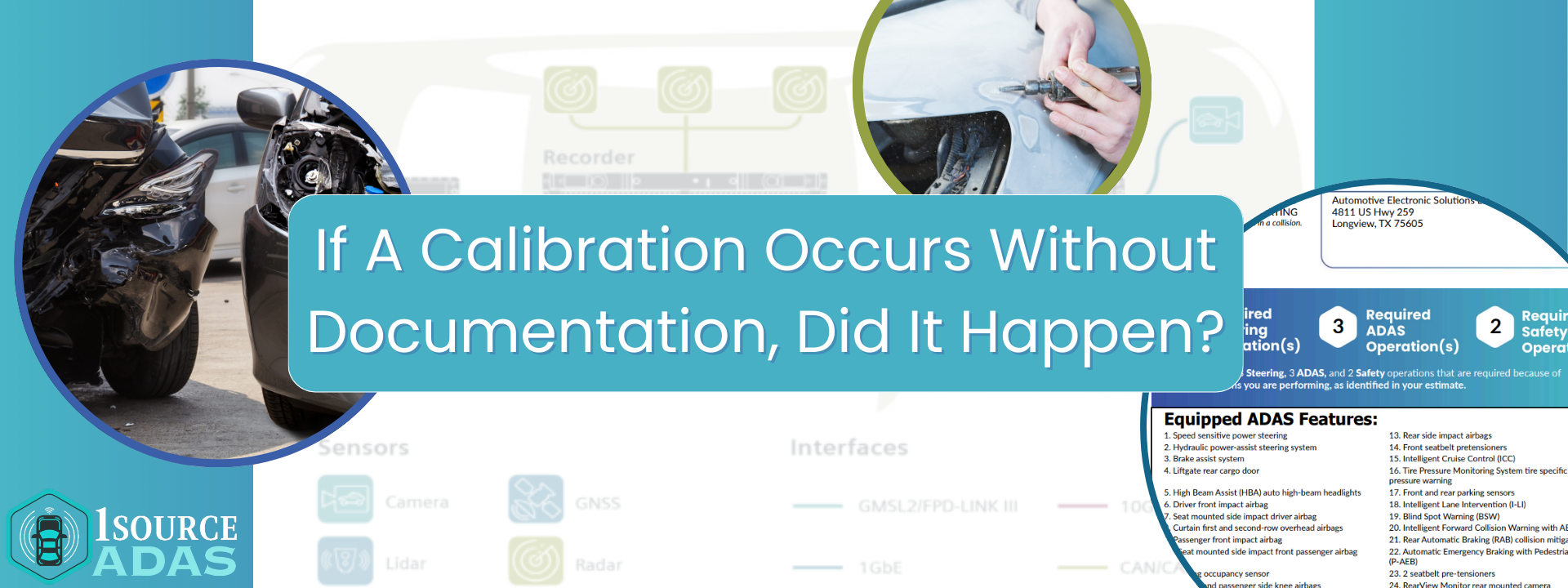
As Advanced Driver Assistance Systems (ADAS) become standard in modern vehicles, documenting these repairs has never been more critical. Proper documentation ensures you are compensated fairly for your services. But this isn't just about getting paid; it's about protecting your customer, your shop's reputation, and mitigating potential liability issues.
Why Proper Documentation is Essential
Proper ADAS documentation should be integrated into the collision repair blueprinting process. While subletting the work to a qualified vendor is common, documenting it the same way you would document sending a vehicle out for an alignment is insufficient. ADAS calibration can be highly technical, time-consuming, and expensive. If an operation is worth putting on the estimate, it is worth having supporting documentation to back up its necessity.
What is ‘Documentation’ Anyway?
We often hear about the importance of documentation, but what does it really mean? Documentation includes all documents, notes, and photos supporting an action was needed or completed. Good documentation practices ensure that this information is seen and used effectively. As a shop, we should document to protect ourselves from future liability, educate our customers about what was done to their vehicle, and support our repair decisions to insurers for correct payment. This requires a central repository of information, typically the estimating system. Complete estimates, repair procedures, and notes of each conversation with the customer and insurer are critical pieces that should be in the file. A good rule of thumb is: ‘If it’s not in the file, it didn’t happen.’
Establishing a Good Documentation Process for ADAS
So, what constitutes a good documentation process that properly addresses ADAS? Let’s break it down.
The Initial Inspection
The primary goal at this stage is to educate and set customer expectations. During the initial inspection, the estimator should meet with the customer, identify and document as much damage as possible, and explain the repair process. It's crucial to inform the customer about potential hidden damage that may only become apparent after disassembly. Discuss the ADAS systems that might be affected by the collision based on damage and educate the customer on what these systems do and how they impact daily driving. Documentation collected in this stage should include the initial estimate, photos, and notes detailing the discussion with the customer.
Blueprinting
The blueprinting phase captures the full scope of the repair. Blueprinting involves writing a complete estimate, usually by a technician and estimator working together on a disassembled vehicle to identify all damaged components and procedures required for proper repair or replacement. This is when all necessary ADAS calibrations are identified, and required safety inspections are completed and documented. The blueprinting process is complete when all damage and necessary replacement components are identified, required sublet and additional operations are noted on the estimate, and supporting documents such as OE requirements, procedures, and photos are in the file.
Blueprinting allows you to get the repair documented in a complete a timely fashion and will eliminate or at least minimize supplements. This lets you present the entire scope of the repair to both the customer and insurer BEFORE you've ordered parts or otherwise committed to an operation which you may not be paid for.
If your shop does not have a blueprinting process, it cannot be overstated how essential it is to a smooth, complete, functional repair process.
Documentation During the Repair
After blueprinting, the repair plan should be set, but the documentation process is ongoing. Communicate the repair plan with the customer and insurer, with notes detailing those discussions in the file. Additional photos documenting milestones and adherence to OEM procedures are recommended as the vehicle progresses through the repair stages.
Typically, calibrations are completed after collision repair and refinishing. If your location uses a sublet method for ADAS service, scheduling these services while the vehicle is in refinish can help avoid delays. Correct blueprinting ensures that the customer and insurer know and approve the required operations.
Final Stages and Customer Notification
As the repair nears completion, documentation remains crucial. Conduct a comprehensive final QC check before releasing the vehicle. A final QC is not just an estimator ensuring there's no compound on a panel in the parking lot; it's a thorough review of the estimate to ensure all listed operations are completed.
Once everything checks out, notify the customer that their vehicle is ready for pickup. Document the completed quality check in the file, ideally with an SOP QC checklist that can be repeated for every repair.
And don’t forget to make sure there’s no compound on any of the panels.
Final Thoughts
“Because it needs it” is no longer a sufficient explanation for an operation. To build trust with our customers, we must explain what we are doing and why we are doing it and support our assertions with manufacturer documentation. Proper documentation can either put you above reproach or completely sink your credibility.
Streamline Your ADAS Documentation with 1Source ADAS
One way to improve your documentation and timely capture of ADAS operations is to utilize a tool like the 1Source ADAS platform. Our AI-powered system can read your repair estimate and provide links to required calibrations, pre-calibration requirements, and safety inspections pertinent to your repair.
Try the 1Source ADAS platform free for seven days when you sign up at
1Source ADAS. Ensuring you find the relevant, required operations for a repair has never been easier!